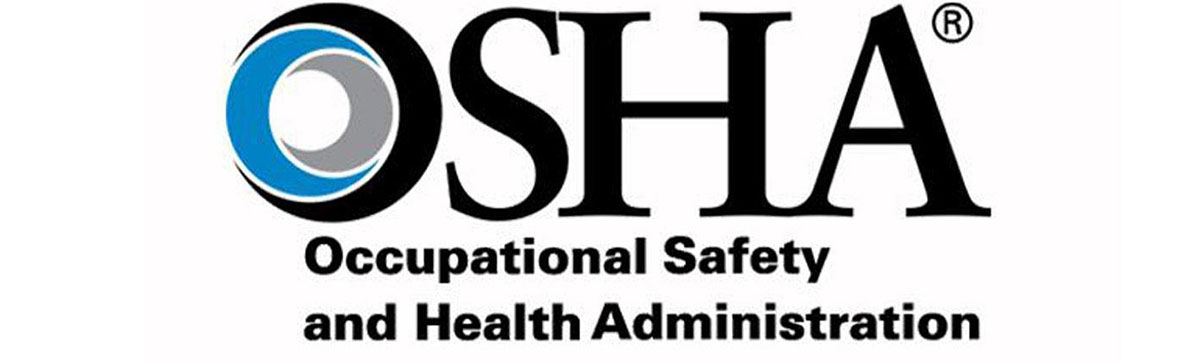
When respirators, including PAPRs, are used to reduce inhalation exposures, OSHA requires a written respiratory protection program in compliance with OSHA 29CFR1910.134 and the respirators must be NIOSH-approved. To be considered NIOSH approved, the PAPR assembly cannot be modified from its approved configuration and only those replacement parts specified and provided by the manufacturer must be used. The manufacturer’s PAPR instructions are specific to a respirator model’s materials and specifications. Instructions are generally provided with the PAPR facepiece, blower, and battery packaging. All instructions must be carefully followed.
OSHA also permits employers to use the cleaning recommendations provide by the manufacturer of the respirator, provided such procedures are as effective as those listed in Appendix B-2, meaning that the respirator is properly cleaned and disinfected in a manner that prevents damage to the respirator and does not cause harm to the user (i.e., skin irritation).
PAPRs may be used in healthcare for a variety of applications. Because they provide higher APFs than N95 FFRs and reusable elastomeric half facepiece respirators, PAPRs are suitable for use when aerosol-generating procedures are performed by hospital first receivers, or when the respirator user is not able to wear a tight-fitting respirator. For effective use, PAPR manufacturer instructions must be followed.
The components of NIOSH-approved PAPRs vary considerably among manufacturers and they react differently to cleaning and disinfection solutions and procedures. Manufacturers’ cleaning and disinfection solutions procedures also vary. These important maintenance activities can cause damage or deteriorate PAPR facepieces, headgear components (hoods, helmets), breathing tubes (hoses) and batteries. If cleaning and disinfection solutions and procedures are ineffective, HCP may be at risk of contact transmission. For these reasons, manufacturers generally recommend that the filter be discarded. Some employers may be able to follow manufacturer-specific instructions for conventional use but the cost of doing so may make PAPRs a less desirable solution to achieve the necessary protection.
Stay the course, stay strong, stay well, mask up and stay tuned!